Do you know about how Dewalt drills are made???? Last year I had the occasion to visit a Dewalt office in Charlotte, North Carolina. I can see with my own eyes how they invent the best instruments in the world from their factory. The opportunity to visit one of the best factories in the world was really awesome. And from this, I can understand why they are one of the best factories in the world. In this article, I will discuss how they can make the best drills in the world.
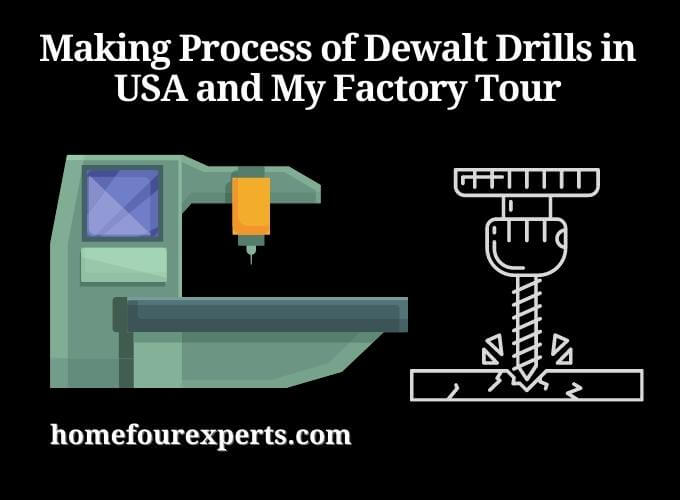
Making Process and My Factory Tour
Do you know Dewalt? It is one of the famous tools for making the company brand in the world. It is one of the best tools for making a company and a famous brand. Most of the country uses its products. I watched the process of making Dewalt a brushless drill. In this section, I am talking about each step of the Dewalt drill making process.
Motor Building
The whole factory is divided into several parts. The motor is made in one part of the factory. The motor is the main part of any power tool. I especially liked the motorized part of the whole factory visit. The Dewalt factory manufactures motors using modern machinery without the touch of a hand.
In the blink of an eye, these robotic devices make peas for the drill. The engines are somewhat worked prior to being twisted with magnet wire at the Dewalt plant. Once the motor is made, it is checked whether the motor is effective. Here it is seen that the balance of the speed of the motor is correct. If any problem is found in the motor, it is allowed to be fixed immediately.

Brushless Drills
In this section, other parts are attached to the DCD995. To begin, the engine and switch get together. The DCD995’s brushless engine may be little, yet it sneaks up suddenly. Presently pre-gathered and pruned switches get together. Look how the gadgets of the switch are completely pruned. This furnishes stun opposition and should assist with sturdiness and security against vibrations.
It may likewise serve to shield the gadgets from dampness or trash. A professional technician segments together all parts by hand. The three huge wires, likely conveying high force from the battery pack, are welded, while the engine control wiring is appended with fast plastic connectors.
One part gets a touch of warmth contract fixed around it, and a Porter Cable warmth firearm is utilized to do it. There’s likewise that red-covered needle-pointed segment distending from the back of the brushless engine. The heatsinked connector and that redback segment are put close to one another. Brushless engines have lobby impact sensors for position detection. supervisor for some knowledge.
Assembly Process
When the guts are prepared, the drill’s infusion formed lodging is prepared. This also is produced somewhere else. So to prepare, the two parts are essentially isolated and put on a holding dance.
The gearbox, electronic grip, and throw, all in a one-piece gathering constructed somewhere else, is passed alongside the lodging.
Let’s talk about the second part of the drill lodging? It’s helpfully put away in the space underneath the forming apparatus until it’s required. Must segments together in the correct manner so that all parts are carefully associated and situated. On the last part of the drill LED PCB that is situated and also the grip is associated with the control switch hardware by methods for a 3-pin connector.
Step by Step Setup
In this part, I will describe how to finally set it altogether. Notice carefully all the 4 final steps for making the Dewalt brushless drill. The two pieces of the lodging are attached together in two phases.
Probably To hold things together all part tidily four screws are fixed on the drill,
At that point, 4 more screws have put the front of the drill, through the gearbox, to get together, interfacing it to the back lodging.
At long last, again 4 additional screws are set on the side.
This is totally finished with drop-down pneumatic screwdrivers that have pre-set force. They’re tranquil and fix the latches rapidly and to the correct force without fail. For the transmission, a more drawn out piece is utilized to get to the clasp.
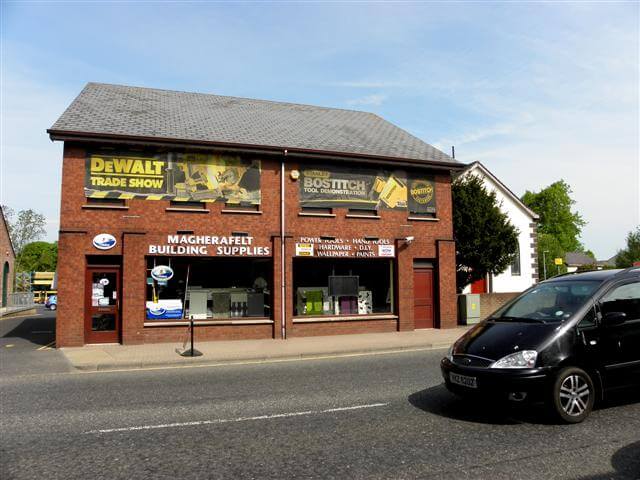
Quality Control Unit (QC), Labeling & Packaging
Once the drill machine is fully set up and programmed, it is sent to the Quality Control Unit. The drill machine is thoroughly checked after coming here. Here it is seen whether every part of the Dewalt drill machine is working properly. No part is left out of the check. From the experience of the Dewalt drill factory visit, it is clear to me that they look at every fold of the QC with great efficiency. If there is a problem with any drill machine in the QC unit, it is immediately removed.
Labeling is done after passing the exam from tuition. Labeling is done after passing the exam from QC. I like the leveling process. After leveling, the computer checks to see if it is in the right place.
Packaging work begins after the Dewalt drill is finished labeling. Part of the packaging is inside the drill box with a battery, a charger, a side handle, and a menu.
Conclusions
Thank you so much for taking the time to read the whole article. Hopefully, I have been able to present my experience to you. And also through this, you know the making process of Dewalt drill in the USA. From the experience of my factory visit, I can assure you that the Dewalt products are the best. They take every step in the process of making any product efficiently. You can nicely do any of your projects with their products.
Read more:
- A Guide for Portable Table Saws for Fine Woodworking
- Experts Analysis and Comparison of Top Ratchet Wrench
- 7 Table Saw Workstation Plans You Can DIY Easily
About This Writer

Hello, I am David Rowan. I am a professional contractor with 10 years of experience in home building, different tools used, construction, home remodeling, and other home improvement work. I have already built many custom homes and continued to do several woodworking projects along with how to deal with all categories of tools.