Contact wheels are a wonderful addition to any grinding arsenal; thanks to the fast change spigot, switching between a flat plate and your contact wheels is a breeze since they both utilize the same tooling arm!
To keep personnel safe and production efficient, urethane and rubber contact wheels are intended to protect your belt grinding machines and finishing equipment. The wheels are available in a variety of stiffness and serration levels, as well as various sizes to suit your demands.
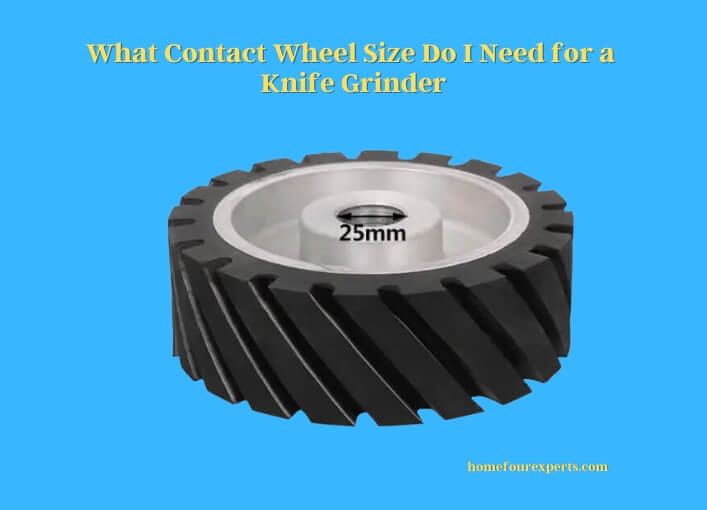
A contact wheel is essential for hollow grinding knife blades, but they’re also great for fast, smooth grinding. According to a grinder, everyone has their own thing and contact wheels. The most common sizes are probably 8 and 10 inches.
How to Assemble a Belt Grinder Contact Wheel
Contact wheels are an indispensable factor for achieving perfect results when belt grinding. Contact wheel and grinding belts need to be made compatible: hard X-belts for hard contact wheels and soft J-belts for soft contact wheels.
The installation of this contact wheel is nearly effortless. Here is how you can do it-
Dress a Contact Wheel
Use a fresh piece of abrasive (ideally resin bond, 50-120 grit) wrapped or held on a flat board to dress a contact wheel. The board should be long enough to stand on one end on the floor and extend above the wheel on the other.
How Often Should a Grinding Wheel Be Dressed?
Tools for dressing that are dull To make a dull wheel, glaze the wheel face. Rotate the single-point or cone-point tool 1/8 turn at regular intervals to retain a well-defined and sharp diamond point. The frequency of these rotations may vary depending on how frequently you dress, but once per day is a decent starting point.
What Contact Wheel Size is Best for 2×72 Belt Grinders Compared to Other Belt Grinder Sizes?
When it comes to the best belt grinders, the ideal contact wheel size for a 2×72 belt grinder is typically 8-10 inches. This size allows for optimal belt coverage and efficient material removal. Compared to other belt grinder sizes, the 2×72 with the right contact wheel size offers superior versatility and precision.
Wire a Grinder Wheel
Using the Angle Grinder to Attach the Wire Wheel
- Unplug or remove the battery from the angle grinder to disconnect it from the power source.
- The angle grinder wheel should be locked.
- Remove the nut that holds the lock in place.
- Remove the current disk from the spindle.
- Turn on the grinder after connecting it to the power source.
Multiple Contact Wheel Sizes
Contact wheels drive abrasive belts and give backup assistance. Contact wheels come in a wide range of face shapes, materials, and sizes. Contact wheels are available with an abrasive belt, and their hub design versatility allows them to be customized for a variety of applications. Contact wheels come in a variety of shapes and sizes. Machine wheels, steel wheels, rubber wheels, plastic wheels, and chain support wheels are all examples.
A contact wheel and coated abrasive belts are used to control unit pressure and speed against a workpiece on a variety of grinding, finishing, and polishing machines. A machine wheel is a component found in heavy machines that perform tasks including deburring, abrasive jet cutting, and water jetting. Steel wheels are sturdy, easy to repair, and inexpensively produced, and they may be painted several times.
A metal or alloy center is always provided with a rubber wheel, which is commonly used in automobiles on the road. A plastic wheel fits the fundamental requirements of a winter tire package and is available in black at a cheap cost of the material. The top of a chain support wheel is where smooth wheels travel over chains. There are a variety of other contact wheels on the market.
Contact wheels are available in a variety of diameters and sizes. A contact wheel with dimensions of 22 x 1.75 cm is often available. Plastic wheels come in sizes ranging from 6 in. x 1.5 in. to 10 in. x 3.01 in. The load rating of plastic wheels is 50-100 lbs.
A rubber wheel with a load capacity of 250-600 lbs and a wheel diameter of 4 in. to 8 in. can be made. The diameter of a chain support wheel should be between 4 and 30.25 inches, with a load rating of 95 pounds. Steel wheels are typically 20 x 8.5 to 22 x 9.5 inches in diameter and have extremely high load ratings.
Things to Think About Other Than Belt Size
While belt size is important, it isn’t the only element to think about while selecting a belt grinder. When looking for a grinder, there are three more things to consider.
Size of the Motor
When choosing a grinder for knife production, the motor size is one of the most critical considerations. To grind steel successfully, you’ll need a high belt speed and the capacity to apply a lot of pressure to the belt.
If you don’t have a powerful enough motor, you won’t be able to grind effectively. As a general rule, at 72″ in length, 1 horsepower of motor power is required for every inch of belt width. The demand for the motor decreases as the belt length decreases. As a result, lower belt lengths need less power.
A 2×72 grinder, for example, would benefit from a motor with at least 2 horsepower. A 2×48 grinder, on the other hand, can function effectively with a 1.5hp engine due to the shorter length of the belt.
Speed of the Belt
Steel grinding necessitates a faster belt speed than wood grinding. As a result, steel stock removal rates will be slower on grinders designed for wood. Depending on the kind of metal, the belt speed (measured in surface feet per minute) will need to be between 4,100 and 7,000. The following formula may be used to compute belt speed:
sfpm = (π x drive wheel diameter) x motor rpm
Speed Variable
Variable speed choices aren’t available on all grinders, and while they aren’t strictly essential for knife manufacture, they are useful to have. Variable-speed grinders allow you to hog heavy steel at full speed while sanding at reduced rates. You’ll be able to create your knives with greater precision and ease if you can manage the speed.
Can an Oscillating Spindle Sander Be Used for Knife Grinding?
Yes, an oscillating spindle sander can be used for knife grinding. However, it may not be as efficient as a dedicated knife grinder. In an oscillating sander comparison, the dedicated knife grinder is likely to provide better precision and control for this specific task.
Final Words
Contact wheels are an indispensable factor for achieving perfect results when belt grinding. Urethane and rubber contact wheels are intended to protect your belt grinding machines and finishing equipment.
Contact wheels are available in a variety of stiffness and serration levels and various sizes. Contact wheels are used to control unit pressure and speed against a workpiece on a variety of grinding, finishing, and polishing machines. A contact wheel with dimensions of 22 x 1.75 cm is often available.
The key advantage of using a contact wheel is that it is easily configured to cut when needed.
About This Writer

Hello, I am David Rowan. I am a professional contractor with 10 years of experience in home building, different tools used, construction, home remodeling, and other home improvement work. I have already built many custom homes and continued to do several woodworking projects along with how to deal with all categories of tools.